Refrigerated air dryers are essential components in compressed air systems, designed to remove moisture and contaminants from the compressed air. Compressed air is widely used in various industrial applications, such as pneumatic tools, automation systems, and manufacturing processes. However, compressed air typically contains a considerable amount of water vapor, which can cause problems like corrosion, decreased efficiency, and malfunctioning of pneumatic equipment. Refrigerated air dryers play a crucial role in maintaining the quality of compressed air by reducing its dew point, thus preventing moisture-related issues.
How Refrigerated Air Dryers Work
Refrigerated air dryers utilize the principle of cooling to remove moisture from compressed air. The process involves three main stages: compression, cooling, and separation.
1. Compression: In the first stage, atmospheric air is drawn into the compressor, where it undergoes compression. During compression, the air's volume decreases, causing its pressure and temperature to rise significantly. As a result, the air becomes saturated with water vapor, as warm air can hold more moisture than cold air.
2. Cooling: The compressed air, now carrying a high amount of moisture, enters the refrigerated air dryer's cooling section. The cooling process aims to reduce the air's temperature significantly, causing the water vapor to condense into liquid water droplets. The cooling is achieved through a heat exchanger or a refrigeration cycle, where a refrigerant absorbs heat from the compressed air, causing the air to cool down.
3. Separation: After cooling, the moisture-laden air reaches a separator, where the condensed water droplets are separated from the dry air. The separated water is then drained from the system, leaving behind dry and moisture-free compressed air. Depending on the type of refrigerated air dryer, the separated water may be collected in a drain trap or automatic drain valve for disposal.
Types of Refrigerated Air Dryers
There are two main types of refrigerated air dryers: cycling and non-cycling.
1. Cycling Refrigerated Air Dryers: Cycling dryers work on the basis of load demand, meaning they adjust their cooling capacity based on the actual compressed air flow rate and ambient conditions. When the demand for compressed air is high, the cooling system operates at its full capacity. Conversely, during low demand periods, the system reduces its cooling capacity, resulting in energy savings. These dryers are more energy-efficient compared to non-cycling dryers, making them suitable for applications with varying compressed air demands.
2. Non-Cycling Refrigerated Air Dryers: Non-cycling dryers operate at a fixed cooling capacity, regardless of the actual compressed air flow rate. They continuously remove moisture from the compressed air, irrespective of the demand. While non-cycling dryers may consume more energy during low-demand periods, they are simpler in design and more cost-effective for applications with constant compressed air requirements.
Benefits of Refrigerated Air Dryers
Refrigerated air dryers offer several benefits, making them a popular choice for various industrial applications:
1. Moisture Removal: The primary purpose of refrigerated air dryers is to eliminate moisture from compressed air, preventing issues such as corrosion, pipe blockages, and reduced efficiency in pneumatic systems.
2. Cost-Effectiveness: Refrigerated air dryers are generally more affordable and have lower operational costs compared to other types of air dryers, making them an economical choice for many businesses.
3. Simplicity and Reliability: The design of refrigerated air dryers is straightforward, leading to easy installation, maintenance, and operation. They also tend to have longer service life and require fewer repairs.
4. Energy Efficiency: With the availability of cycling refrigerated air dryers, users can achieve significant energy savings, as the cooling system adjusts its capacity based on actual demand, reducing unnecessary energy consumption.
5. Compact Size: Refrigerated air dryers are available in compact designs, making them suitable for installations where space is limited.
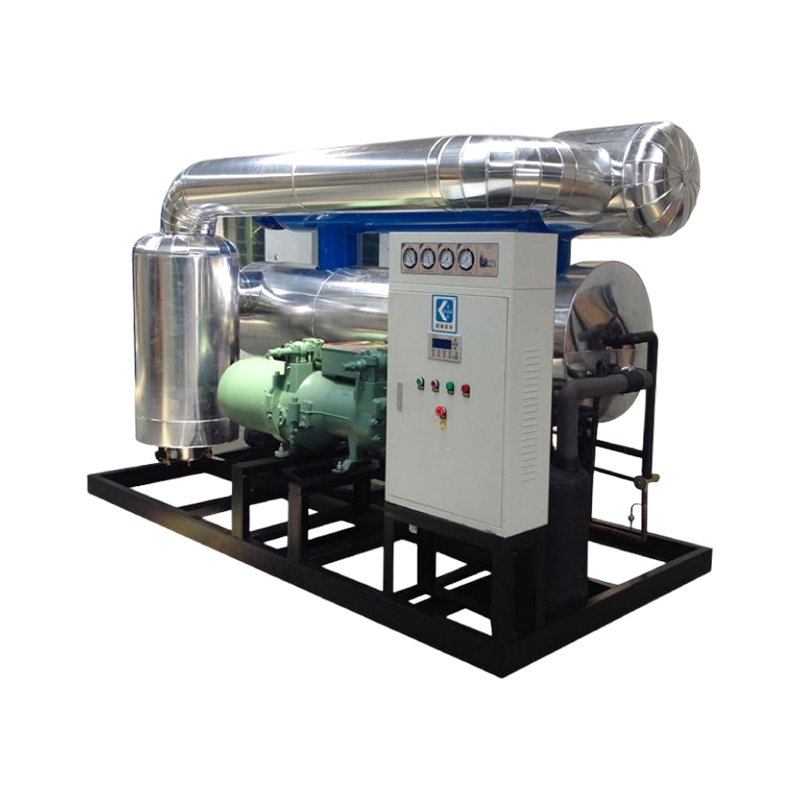
Limitations and Considerations
While refrigerated air dryers are effective in many applications, they do have some limitations and considerations:
1. Dew Point Limitation: The dew point achieved by refrigerated air dryers is typically higher than other types of dryers like desiccant air dryers. As a result, they may not be suitable for applications requiring very low dew points, such as sensitive electronics manufacturing.
2. Pressure Drop: The cooling and separation process in refrigerated air dryers can cause a slight pressure drop in the compressed air system, which may need to be accounted for in certain applications.
3. Ambient Conditions: The efficiency of refrigerated air dryers is influenced by the ambient air temperature and humidity. In high-temperature environments, the dryer may have to work harder to achieve the desired moisture removal.
4. Maintenance: Regular maintenance is essential to ensure optimal performance and longevity of refrigerated air dryers. Proper condensate drainage, filter replacement, and system checks are necessary to avoid potential issues.
Refrigerated air dryers are indispensable devices for maintaining the quality and efficiency of compressed air in various industrial settings. By efficiently removing moisture from compressed air, these dryers prevent corrosion, blockages, and other potential problems in pneumatic systems. While they may have some limitations, refrigerated air dryers continue to be a popular choice due to their cost-effectiveness, simplicity, and reliability. As technology advances, manufacturers are continuously improving these devices, making them even more energy-efficient and suitable for a wide range of industrial applications. When selecting a refrigerated air dryer, it's essential to consider factors such as dew point requirements, compressed air demand, and the operating environment to ensure optimal performance and cost-effectiveness.