Compressed air filters play an important role in ensuring the air in your home is safe to breathe. There are several options when choosing a filter, and it's important to choose the one that suits your needs.
Particulate air line filters are one of the most common types of air filters used in compressed air systems. They remove particles, dirt, water and oil from the air.
When installing particulate air line filters, it is important to remember that these filters should be replaced periodically. This will help the compressor work more efficiently. However, there are many factors that will determine how often these filters should be replaced. Air line filters are rated according to the particle size they are able to remove. The filtration efficiency of a particulate filter depends on the particle size it can capture and the type of media it uses.
Filter media is the main component of particulate air line filters. Media is usually made of fibers that are electrostatically attracted to smaller particles. Smaller particles can be captured by diffusion. If the filter media is damaged, these contaminants cannot be removed.
There are several types of particulate air line filters, including coalescing filters. Coalescing filters reduce oil and liquids up to 0.01 ppm. These filters also remove aerosols from the air stream.
Coalescing filters typically consist of a pressure envelope and a filter element. This element can be a hand drain or a float drain. Most filters are equipped with differential pressure monitoring. In addition to particulate air line filters, there are also chemical air line filters. Chemical air filters can be cartridge units or pressure vessel units. All of these types of filters use activated carbon or some other material to absorb gases or liquids. Activated carbon filters are most commonly used in pharmaceutical and food processing. During the filtration process, thousands of small eddies are created.
An air intake filter is a device that helps prevent dust and debris from adhering to the internal parts of the compressor. When used properly, they can extend the life of your compressor. There are many types of air filters on the market. Each has a different function. For example, high-efficiency air filters can trap pollutants with a low pressure drop. These filters also reduce the energy costs you pay to run your compressor. Choosing the right type of air filter for your needs is crucial. In addition to saving you money, having the right filter can save you from costly downtime.
Air filters come in different sizes and shapes. They are designed to trap dirt, dust and water. A clogged filter can cause a significant pressure drop, which affects the output of the compressor. Choosing the right type can help you get the best results. In fact, you might be surprised how much less energy you expend with a proper filtration system. There are three main types of filters: intake filters, in-line filters, and dry particulate filters. All of these options will remove particles smaller than 0.01 microns. Some are even able to remove oil stains.
Depending on the application, you may need filters with a more specific purpose. Filters for paint and body applications need to be able to remove all particles. You also need to make sure your equipment complies with industry standards. Other options include filters that capture chemical fumes. Activated charcoal, made from charcoal, helps trap these vapors. The absorption process naturally attracts these vapors, making them easier to combine. Air filters are designed for a variety of pneumatic applications. Be sure to consult your company's manual and select the appropriate filter for your needs.
Compressed air filters are designed to remove contaminants such as dirt, oil and water. Finding a filter that works for your system is important. When deciding on a filter, consider how you will be using the air and what kind of contaminants you want to keep out of the airflow. Compressed air filters are generally designed to remove vapors and aerosols. Both types of pollutants can be harmful to people and equipment. They may also cause damage to the product. Adsorption and coalescence are processes used in filter media to separate liquids and gases. Activated carbon is the most common medium used in adsorption filters. However, coalescing elements can more effectively separate gases and liquids.
During adsorption, particles adhere to the surface of the adsorbent. As the sorbent dissolves, the fluid flows from the sorbent to another liquid. Coalescence works by forcing small droplets to collide into larger ones. This makes it easier for smaller particles to be captured by the filter media. Coalescing filters are sometimes used in combination with dry particulate removal filters. The combined system can effectively remove pollutants and mist. However, these filters are not effective in removing vapors and aerosols. Coalescing filters are usually located in the compressor room. They are not as common as dry particulate filters. Depending on the size of your system, you may need a new coalescing element after 6-12 months of operation.
A differential pressure monitoring device is available as an optional accessory. While they're not considered good indicators of air quality, they do provide valuable information about premature filter element clogging.
Coalescing and adsorption filters are used in a wide variety of applications. These filters remove oil aerosols, lubricating oil mist, and gas and liquid mixtures. Compressed air filters are used in a variety of applications. They are capable of removing aerosols, water and oils from air streams. Fine coalescing filters are often the first line of defense against air pollutants. Oil carryover in transfer lines can be reduced from 5 mg/m3 to 1 mg using coalescing filters. The coalescing process also prevents re-entrainment of large droplets.
Selecting the best type of filter element for your application is a critical step in optimizing your air handling system. Filters are divided into three basic types: particulate filters, vapor removal filters, and activated carbon filters. Each category has different performance and cost.
A particulate filter element traps coarse particles. These filter elements are usually made of sintered material. The intake filter removes coarse particles such as dust and pollen. Likewise, the fine filter removes particles as small as 1 micron. Activated carbon filters are commonly used to remove hydrocarbons. They are used in a range of applications such as food processing, pharmaceuticals and respiratory. The coarse particle filter removes particles as small as 5 or 40 microns. They are commonly used for painting and mainline plant filtration. Coarse and fine coalescing filters are typically implemented at the point of use. In contrast, vapor removal filters are often installed with particulate filters.
Activated carbon filters can help remove hydrocarbons and oils from compressed air. They are commonly used to produce breathable air, but they are also an essential step in the process of mixing medicines and foods.
Coarse coalescing filters reduce the volume of lubricant aerosols that can quickly saturate vapor removal filters. Likewise, fine coalescing filters can be used in painting and other applications where the presence of lubricant aerosols can damage products or cause equipment inefficiencies.
Activated carbon filters for compressed air are designed to remove airborne pollutants such as chemicals, vapors, and odors. They are used in a wide range of applications from industrial plants to medical facilities.
Unlike other air purifiers, activated carbon filters work through an adsorption process. This means that contaminants stick to the carbon surface and are then removed. Carbon filters can also be used as pre-filters to trap large solid particles.
Carbon air filters are an important part of a home air purification system. When used in conjunction with HEPA filters, they can remove various organic compounds and VOCs from the air. Activated carbon filters for compressed air come in many different forms. Typically, they are made of composite carbon materials. Other forms include granular activated carbon (GAC), powdered activated carbon, and beaded activated carbon. Generally speaking, the larger the micropore volume of carbon, the better the filtration effect. This is because it provides a larger surface area for the adsorption of pollutants.
Some more modern forms of activated carbon filters for compressed air are made from deeply pleated polyester. These filters are non-corrosive and capable of operating at temperatures up to 66 degrees Celsius. Also, they can be reused. Activated carbon filter removes odors, oil vapors and chemical vapors. They are commonly used in the manufacture of food, pharmaceuticals and other industrial applications. The main function of carbon air filters is to remove organic compounds from the air. They also have the ability to absorb odor molecules. This filter can be used to treat small residential applications, as well as larger community water systems.
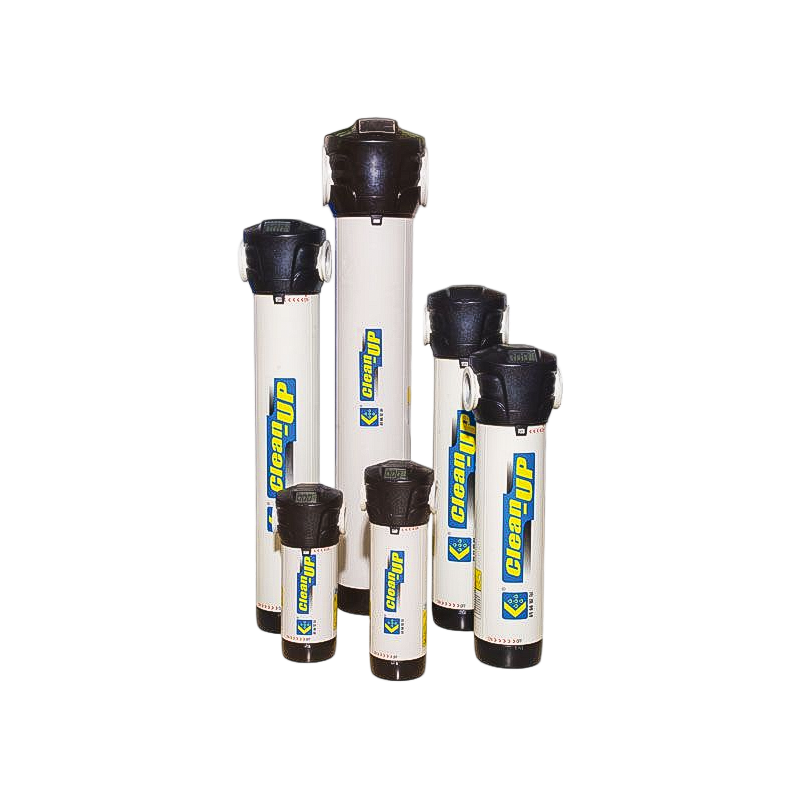
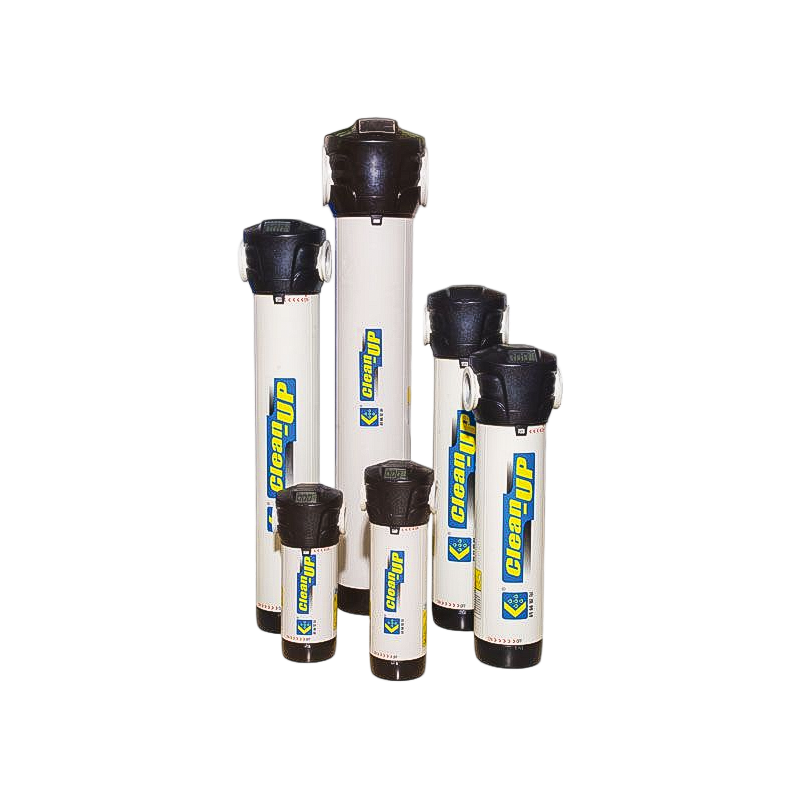
1.035-800 type filter element is adopted of aeronautic diversion technology, the air inlet is designed to a smooth 90°elbow which can greatly reduce the turbulence and pressure loss.
2.Adding a cone-shaped flow diffuser at the bottom of filter element, flow diffusion increases the filtering area.
3.Adopting bayonet type installation, easy to replace the filter element.
4.Imported high performance glass fiber materials
5. Filter house is aluminum alloy material, max pressure is 16bar.