Compressed air dryers are essential components in compressed air systems, designed to remove moisture from the air to prevent damage to equipment and ensure efficient operation. There are several types of compressed air dryers, each employing different mechanisms to achieve moisture removal. Let's explore the different types and their working principles:
Refrigerated Air Dryers:
Refrigerated air dryers are the most commonly used type of compressed air dryers. They utilize a refrigeration system to cool the compressed air, causing moisture to condense and separate from the air stream. The condensed moisture is then drained out of the system. The cooled and dried air is then reheated to prevent condensation in downstream pipes and equipment. Refrigerated air dryers are effective in achieving dew points around 35°F to 50°F (1.7°C to 10°C), suitable for most general industrial applications.
Desiccant Air Dryers:
Desiccant air dryers use a desiccant material, typically silica gel or activated alumina, to absorb moisture from the compressed air. These dryers employ two towers filled with desiccant beads. One tower is in the drying mode while the other undergoes regeneration. The wet compressed air passes through the drying tower, where moisture is adsorbed by the desiccant material, resulting in dry air. Meanwhile, the regeneration tower is depressurized and heated to remove the moisture from the desiccant beads, preparing it for the next drying cycle. Desiccant air dryers can achieve extremely low dew points, making them suitable for applications with stringent moisture requirements.
Membrane Air Dryers:
Membrane air dryers use a permeable membrane to separate moisture from the compressed air. The membrane has tiny pores that allow water vapor molecules to pass through while blocking larger air molecules. As the compressed air passes through the membrane, the moisture permeates and is discharged, leaving dry air behind. Membrane air dryers are effective in removing water vapor but have limitations in achieving low dew points. They are often used in applications where moderate dew points are acceptable, such as instrument air systems.
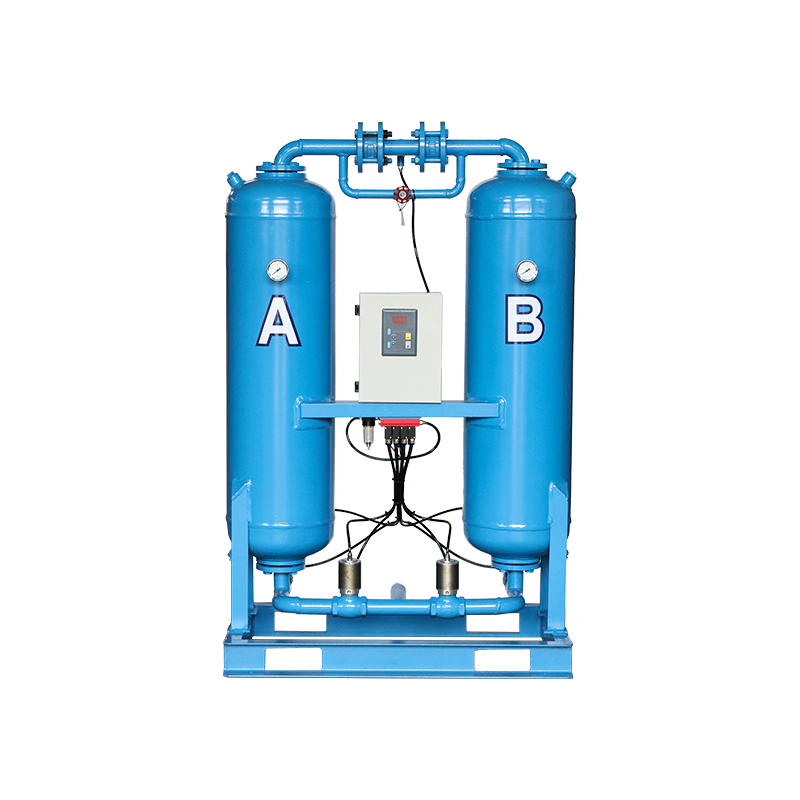
Heatless Regenerative Air Dryers:
Heatless regenerative air dryers operate on the principle of adsorption and regeneration using desiccant materials. Similar to desiccant dryers, they use two towers filled with desiccant beads. However, instead of external heaters, the regeneration process is achieved by depressurizing one tower and allowing the pressure drop to release the moisture. The dry tower then switches to the drying mode while the regenerated tower takes over the moisture removal process. Heatless regenerative dryers are energy-efficient but have longer regeneration cycles compared to heated types.
Heated Regenerative Air Dryers:
Heated regenerative air dryers utilize a combination of heat and desiccant material to remove moisture from compressed air. These dryers use a heater to regenerate the desiccant material, ensuring a more efficient moisture removal process. The regeneration process involves passing a small portion of dried air or external heated air through the tower containing the desiccant material, removing the moisture and preparing it for the next drying cycle. Heated regenerative air dryers can achieve low dew points and are commonly used in critical applications where consistent dry air is required.
In conclusion, compressed air dryers play a vital role in removing moisture from compressed air systems. Different types of dryers employ various mechanisms, including refrigeration, desiccant adsorption, membrane separation, and regeneration processes, to achieve moisture removal and provide dry air for specific applications. Selecting the appropriate type of compressed air dryer depends on the desired dew point, application requirements, and energy considerations.