Desiccant air dryers offer manufacturers an immediate and economical way to protect equipment, reduce maintenance costs and reduce their carbon footprint.
For many industrial operations, it is critical that pneumatic equipment be in an environment with a clean and consistent supply of compressed air. In addition to affecting energy bills and production costs, contamination from water, dirt or dust can lead to poor equipment performance, failure, component corrosion, cylinder and solenoid valve failure, and air tool damage.
Condensation and corrosion can disrupt manufacturing in various industrial sectors including food, beverage, pharmaceutical, marine and aerospace. Compressed air dryers as well as refrigerated dryers to ensure the air reaches the desired dryness.
A typical desiccant air dryer pays for itself in less than a year by reducing and eliminating maintenance costs and downtime, increasing the efficiency of company operations while reducing shipping emissions and reducing environmental impact through service calls and disposal of broken parts.
Dry air keeps pneumatic equipment running at peak efficiency and extends the life of air tools, motors and cylinders. Desiccant dryers pass compressed air through a pressure vessel with two "towers" filled with beds of alumina desiccant. This is the material that absorbs moisture from the air and the bed becomes saturated and regenerated in the next cycle
The dryer switches towers regularly according to a standard timing cycle. During the drying cycle, some compressed air is used to purge/dry the reduced pressure desiccant off-line bed. Adsorption air dryers are available in electric and pneumatic control forms, controlled by PLC with reliable touch screen.
Air flow can be from 100 SCFM to 10,000 SCFM and pressure from 100 psi to 500 psi. A certified lifting frame is available as well as a multi-stage filtration system for maximum protection. AS-1210 or ASME V111 ram pressure valves are available and the system features an ultra-quiet silencer for noise control.
Desiccant air dryers are designed for a consistent pressure dew point (-40°C to -60°C) to eliminate moisture and freeze at low ambient temperatures. The system is fully assembled, plumbed and wired, and filled with activated alumina desiccant. The only operation required is to connect the system to the utility.
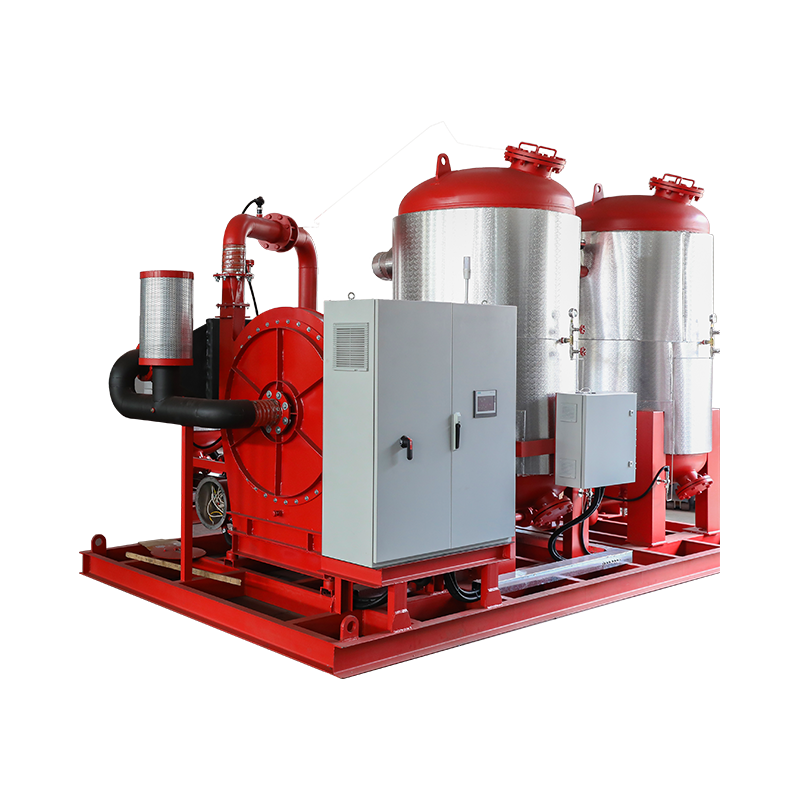
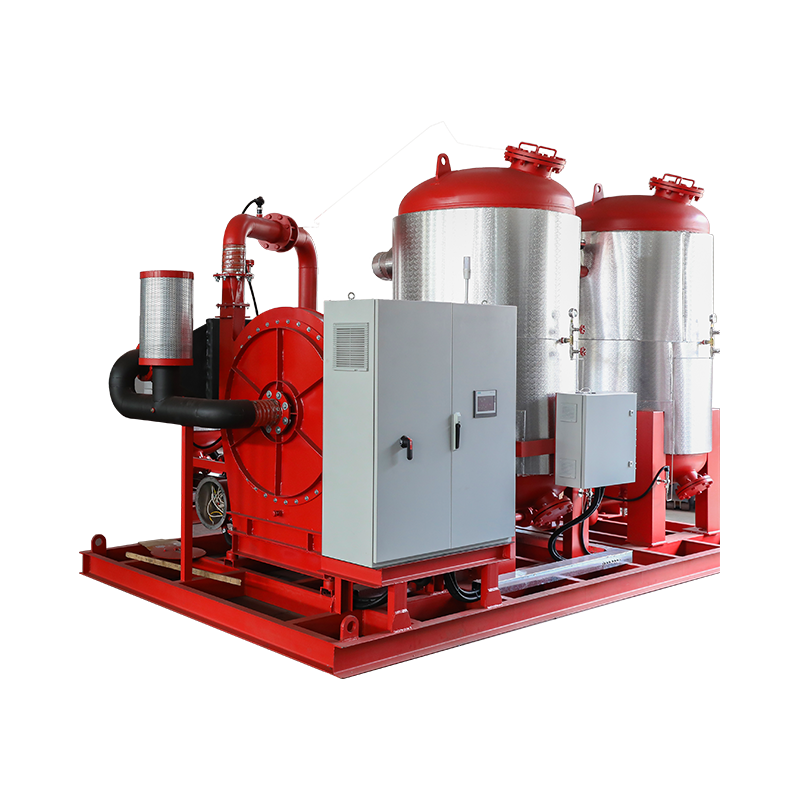
KXB series heated blower purge regeneration air dryer uses air blower and external electrical heater to produce purge air for desiccant regeneration. The blower intakes atmospheric air flow through the heater, then through the desiccant media thereby regenerating it. With this design, no dried compressed air is consumed for regeneration, which maximizes the amount delivered to the air system. Blower heater Air Dryer is usually suitable for large flow from 15 -510m3/min ,2~3% airloss, outlet air pressure dew point is -40~ -70°CPDP. System with Siemens PLC controller, with touch screen,Dew-point sensor.
For higher grade, we also could provide KXP Non purge blower desiccant dryer.