Oxygen membranes are a great way to produce nitrogen from methane gas. This is because the membrane allows you to produce nitrogen by mixing two gases. By doing this, you produce more nitrogen, and more quickly. Therefore, there are many benefits to using an oxygen membrane. Here are some:
Oxygen-permeable membranes are a promising strategy for improving nitrogen production efficiency in power cycles. However, polymeric membranes are generally not capable of high permselectivity. This study aimed to examine the effect of the surface roughness of these films on their performance.
A BCFZ hollow fiber membrane reactor was used in this study. Generate a porous layer using the BCFZ slurry heated at 1050 °C for one hour. Then brush it on the outer surface of the membrane. After 120 h of operation, analyze the SEM images. These results indicate that the porous BCFZ layer increases the oxygen ion association sites, thereby increasing oxygen permeation.
Fe-pillared Cloisite 15A (P-C15A) dispersed in a polysulfone matrix. It has many properties including kinetic diameter, pKa and selectivity.
Using image analysis software, estimate the left-right contact angle of the membrane. Roughness is an important factor in determining the mechanical strength of the membrane and the performance of the system.
At 890 °C, the membrane showed high selectivity for carbon dioxide and methane. However, in the presence of lithium chloride, this value was reduced by 63%.
As the methane concentration on the permeate side increased, the methane conversion decreased from 45% to 33%. This decrease may be attributed to the reduced rate of 1O2 mesenchymal formation within the membrane.
In addition, the porous BCFZ layer can enhance the oxygen transmission efficiency. The lower limit of 1O2 permeability is only 2 cm/s. Although the oxygen transmission rate was slightly higher in the presence of the porous layer, it was not enough to achieve complete conversion of methane.
A membrane oxygen plant is an industrial system designed to generate oxygen. It is relatively simple and reliable, and can be integrated into existing air systems. Membrane oxygen plants produce 30-45% oxygen purity. This is the main advantage over other plants.
Oxygen is essential for aerobic organisms and is present in a variety of technological processes. For example, it is widely used in the oil and gas sector to process and increase the viscosity of oil. In addition, it is used in cutting processes and brazing processes.
Traditionally, measurement methods have relied on colorimetric analysis, but recent developments allow real-time data. A method called O-OCR allows the simultaneous detection of oxygen consumption across multiple membrane bilayer devices.
Another method, O-MCP, allows simultaneous collection of oxygen concentration and oxygen consumption data. Initially, this was done with a single device. Using finite element analysis-based modeling, researchers were able to simulate measurements and estimate single-cell OCR data.
The optical-based sensor unit is located in the bottom microchannel of the O-MCP. The sensor unit is 0.75mm thick. The flow in each microchannel is controlled by an array of micropumps located within the lid of the device.
O-MCP also allows the measurement of drug-induced metabolic changes. These changes were monitored in microfluidic culture plates containing human kidney proximal tubular epithelial cells.
Because membrane oxygen concentrators are easier to operate, they cost less to operate. In contrast, cryogenic oxygen plants require more advanced technical equipment and are more complex to operate. However, these plants are more reliable and can provide higher purity oxygen.
In this study, the optimal structural design of the OTM module was determined by identifying relevant geometric parameters. This is an important step towards demonstrating an oxygen membrane module that can be successfully assembled, tested and operated in an industrial setting.
For this purpose, a prototype module was designed using a multidisciplinary approach. This requires consideration of factors related to manufacturing process, assembly, characteristics and design. It is worth noting that this approach can be extended to other types of modules. The key to a successful design is having the correct sealing system.
The components used in this study are plate-type OTM modules constructed of composite ceramic materials and porous layers. Each layer is laminated together to form a unit. Design internal passages for reasonable gas flow rates.
A 20-node hexahedral element was added to the model to improve the accuracy of the Thin Film OTM module. This increases the precision of the stress values on the gas channel layer.
Several penetration tests were performed to assess the effectiveness of the membrane. One of the most successful of these tests showed that the most effective permeable area was actually at the top of the porous layer.
Methane is an important component of natural gas. It is produced by many processes such as wastewater treatment, landfills, anaerobic digestion, land use and transportation of fossil fuels.
CH4 emissions per unit area depend on the soil type and the concentration of CH4 in the soil. It is estimated that between 50% and 90% of the CH4 produced underground is oxidized before reaching the atmosphere. This is due to the presence of pore space and the ability of microorganisms to oxidize gases.
Methane can be an effective warming agent. However, its warming impact diminishes over time. Fortunately, many of the pollutants associated with this short-lived gas can be reduced or eliminated by improving oil and gas equipment and reducing leaks.
Additionally, natural wetlands and wildfires are sources of methane. As this gas is highly flammable, it may form explosive mixtures with air in poorly ventilated spaces. These explosive mixtures can cause severe respiratory illness.
Another major source of methane emissions is the burning of fossil fuels. EPA developed a coalbed methane promotion program to help address this issue. By upgrading oil and gas equipment, preventing spills and educating the public, the agency hopes to reduce this pollutant's contribution to our climate.
A two-year field trial was conducted in southeastern China. The study examined the interaction of different soil layers and methane emissions. The CH4 concentration in the different layers was measured using a multi-stage sampling probe.
The effect of nitrogen fertilization on soil CH4 concentration was studied. The CH4 concentration in the four-layer soil increased with nitrogen fertilization. Biochar correction had no significant effect on CH4 concentrations.
The aim of this study was to investigate the permeation of oxygen through an asymmetric membrane. It also attempts to identify challenges associated with producing promising membrane materials.
Oxygen permeability is important in determining the economic viability of a membrane process. In order to develop efficient, environmentally friendly and sustainable solutions for oxygen production, membrane materials must have high oxygen permeability. This is critical for improving process efficiency and reducing production costs. Various studies have investigated the permeability of oxygen in different membranes.
Permeability is a function of the oxygen partial pressure gradient, the surface exchange rate, and the bulk diffusivity of oxygen ions. However, the impact of these variables may vary depending on the experimental setting. For example, the permeation of oxygen through polymer membranes is often limited by the chemical and thermal stability of the material.
We investigated the effect of temperature and inlet air velocity on the permeation of oxygen through two asymmetric membranes. To determine the oxygen generation rate, we also supplied pure helium as purge gas on the supported side of the membrane.
Our results suggest that oxygen flux increases by an important factor due to increased oxygen permeation. In addition, the nitrogen purity on the core side is also improved. Despite the higher oxygen permeability, the carbon dioxide selectivity remains unchanged.
A series of room temperature tests were performed on a large number of samples. These tests confirm the repeatability of the manufacturing process. At 950 °C, the flexural strength sf was measured using a custom-made four-point SiC fixture. Additionally, a Pt/Pt-Rh thermocouple was placed next to the sample to monitor the temperature.
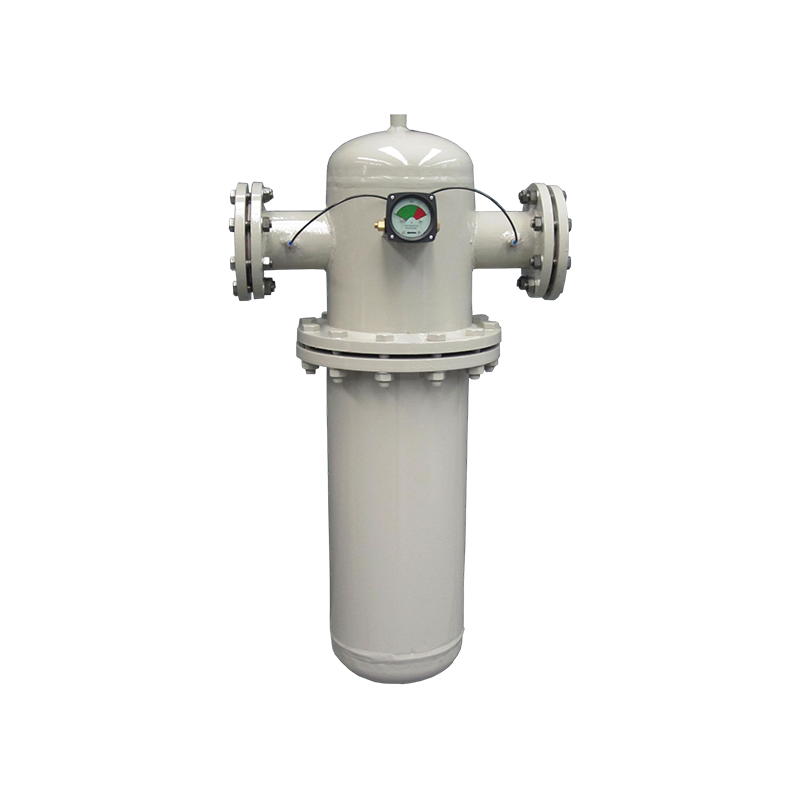
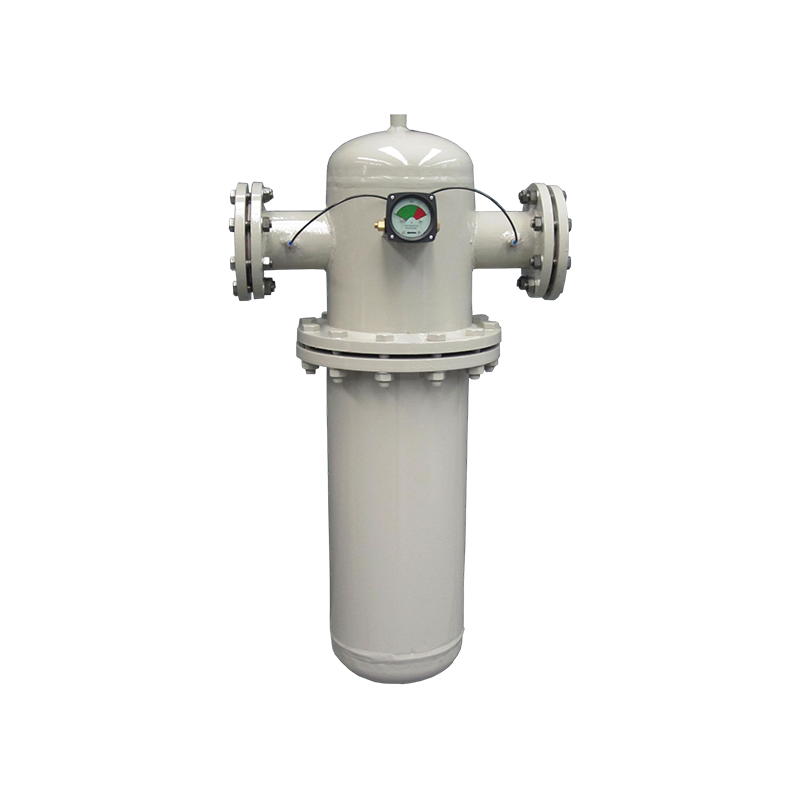
KL company have 5 kinds of compressed air filter for your choose:
CLASS C Main pipe dust filter ----3micron3ppm
CLASS T Main pipe oil/water filter ----1micron1ppm
CLASS A High efficient oil filter ----0.01micron0.01ppm
CLASS F Supper high efficient oil filter----0.01micron0.001ppm
CLASS H Activated carbon micro oil moisture filter----0.01micron0.003ppm