Using a membrane dryer is a great way to maintain the quality of your medical equipment at an optimal level. They can also help you save money by reducing the amount of air used to dry medical products.
Membrane dryers offer a higher level of reliability and durability than other dryers. They are quiet and require low maintenance. They are also ideal for remote operations. They are capable of a pressure dew point of -40 degrees Celsius and are suitable for a variety of stationary applications. They can also be used in hazardous areas.
These dryers use a desiccant to remove moisture from the compressed air. They have four different regeneration techniques. Depending on the type of desiccant dryer, the regeneration process can be facilitated by a timer or dew point monitoring device.
Membrane dryers are often sized for small projects or gas separation applications. They are quieter than other dryers and require no electricity. However, they do require high levels of purge air. This air is needed to remove oil and particulates from the compressed air. They are also susceptible to oil contamination and can be used in hazardous areas.
Generally, the choice of membrane dryer depends on factors such as operating pressure, flow capacity, inlet temperature and oil separation filter requirements. They are widely used in stationary applications such as the automotive, petrochemical and food industries.
There are two types of adsorption dryers: single vessel and double tower. They both use a desiccant to remove moisture from the compressed air.
Using digital purge control with membrane dryers can help you save a lot of energy while getting the job done. That's because digital devices help you control the proper air purge pressure and help you reduce your purge air costs by up to 18%. The unit also has a 5-stage HEPA degreasing pre-filter that removes purge fumes and other contaminants from the compressed air.
A membrane air dryer is a dryer that uses a bundle of hollow fibers to spray dry air. It has no moving parts and doesn't require much maintenance. It is also the newest and most advanced form of compressed air drying. The equipment can be purchased as a standalone, modular or combination unit.
Top models utilize multiple thermocouples to control the process. These thermocouples are capable of providing a continuous temperature display. Auxiliary heater contactors also help prevent equipment from overheating. The best dryers also have a large, light, and efficient heat storage tank. In addition, these devices require less energy to operate. The best dryers also come with state-of-the-art PLC controls that simplify troubleshooting and keep the machine running smoothly.
High temperature drying with a membrane dryer can reduce fuel costs and increase fuel efficiency. Membrane dryers require less equipment than adsorption dryers and can run on very little power.
Membrane dryers use membranes made of hollow polymer fibers. These fibers have a coating on the inner surface that allows water vapor to pass through. The water vapor is then vented out of the cylinder.
Membrane dryers have different types of membranes. They can be classified according to molecular size and gas solubility. They are useful in applications that need to run continuously. They can also be used in hazardous locations.
Membrane dryers use the principle of selective permeation to remove moisture from compressed air. They are used in air bearings, air spindles, air brakes, and medical equipment. Unlike adsorption dryers, membrane dryers do not require an external control unit. They are also quiet and reliable.
Membrane dryers can produce extremely low dew points. They also remove moisture from gas components such as nitrogen. They can also be used to eliminate mold growth. They are easy to install and safe. Membrane dryers are an inexpensive and reliable solution to your drying needs.
To maximize the membrane's drying capacity, you need to consider operating pressure and flow. Membrane dryers are also affected by humidity and temperature.
Using a membrane dryer to lower the dew point of the process air is very effective. A membrane dryer is a device that removes moisture from compressed air by using a four-stage filtration system. These dryers are often installed as point-of-use dryers. They are commonly used in medical, industrial and professional manufacturing environments. These dryers are quiet and easy to operate. They require little direct maintenance and are inherently explosion-proof.
There are several different types of membrane dryers. They include single tower deliquescent dryers and double tower deliquescent dryers. These devices work by using a large pressure vessel filled with salt crystals. Water vapor is forced through the media, forming brine, which drains from the bottom of the vessel.
Membrane dryers are also available for applications requiring continuous operation. This type of drying equipment is ideal for environments where the dew point needs to be consistent. These dryers are also designed to operate passively, making them ideal for remote applications. These dryers do not require power or external control systems. They are also relatively cheap.
Membrane dryers are also available for applications where the air is exposed to freezing temperatures. In some applications, it is necessary to lower the dew point to -40 degrees.
It is critical to keep pneumatic systems free from moisture, which can lead to corrosion, wear of parts and overall equipment failure. Additionally, moisture increases energy consumption and contaminants can build up in your equipment, leading to costly repairs and downtime.
Membrane dryers, in particular, are an ingenious way to draw moisture from the air and are an effective way to prevent moisture from damaging pneumatic equipment. These devices are commonly used in pneumatic systems in industrial environments. They are light and compact and require no external power supply. They can be installed directly into your system plumbing.
Membrane dryers use a permeable membrane to draw water vapor from the air. The dry air is then vented to the atmosphere and recirculated downstream. This process is considered the best way to dry the air.
Membrane dryers produce ultra-clean air suitable for analytical instruments. They are suitable for use in environmental chambers and other low volume air separation applications. They are also ideal for waveguide drying. They are lightweight, require minimal maintenance, and are suitable for low volume systems.
Membrane dryers can be connected in parallel to increase their capacity. They can also be used with micro-mist separators for optimal dehumidification.
Membrane air dryers are used for laser plenum purging. Membrane dryers are common in laboratory and professional manufacturing environments. Membrane dryers are designed to operate continuously and produce high quality dry air. They are also quiet and require no external controls or power.
Membrane dryers are often used in applications that require continuous operation, such as medical equipment. Membrane air dryers also produce extremely low dew points. However, they are not suitable for mainstream applications.
Membrane dryers are suitable for applications requiring continuous operation such as air bearings, medical equipment and pneumatic spindles. Membrane dryers are also used in pneumatic components such as pneumatic brakes and air brakes for trains.
Membrane air dryers use pressure swing adsorption technology to provide clean, dry air. The technology features an advanced purification filter and automatic regeneration. It also features a full post-filtration system. This technology provides cleaner, less polluted air, which helps improve laser performance and lower service costs.
Various types of membrane dryers are used to remove moisture from compressed air. They are suitable for a variety of end-user industries such as pharmaceuticals, food and beverage, and oil and gas. Membrane dryers are also used in medical equipment.
In the medical industry, membrane dryers are used to provide clean, dehumidified air. They are used in various components of medical equipment such as air guns, air shafts and air bearings. Additionally, they are used in laboratory equipment and analytical controls.
The increase in the number of hospitals is expected to accelerate the growth of membrane air dryers. Furthermore, the increasing number of chronic diseases has led to the development of better diagnostic equipment. Moreover, increasing R&D activities are expected to drive the market in the coming years. The overall product market is also expected to benefit from the increasing application of the product in the food and beverage industry.
Membrane dryers are suitable for low volume compressed air systems. They are easy to install and operate. Plus, they are cheap to run and require little maintenance. They are compact, reliable and lightweight. They are also used in various end-use industries including pharmaceutical, food and beverage, and chemical industries.
Membrane dryers are used in a variety of medical equipment such as air guns, air bearings and pneumatic spindles. Additionally, they are used in laboratory equipment including microscopes, spectrophotometers, and laser plenum chamber purging.
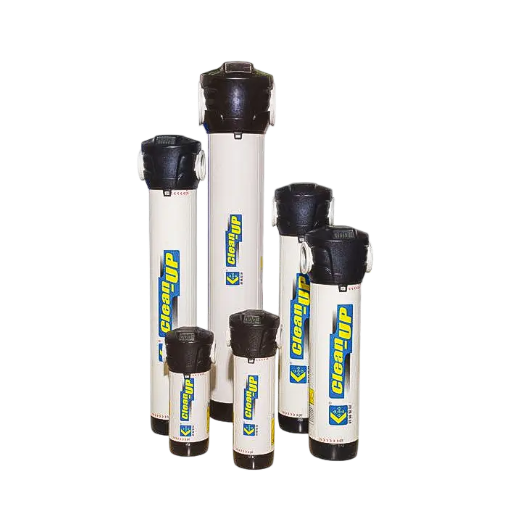
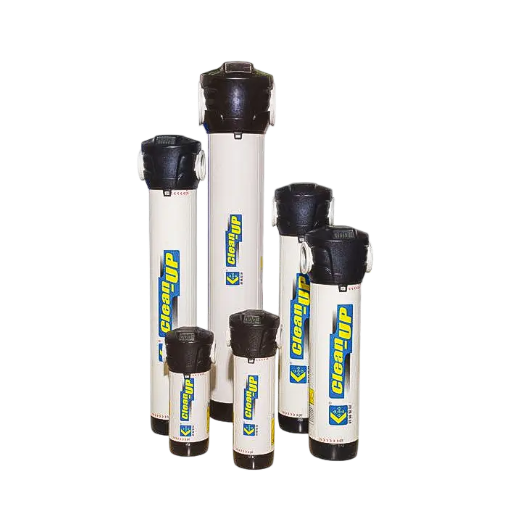
KL Filter
1.035-800 type filter element is adopted of aeronautic diversion technology, the air inlet is designed to a smooth 90°elbow which can greatly reduce the turbulence and pressure loss.
2.Adding a cone-shaped flow diffuser at the bottom of filter element, flow diffusion increases the filtering area.
3.Adopting bayonet type installation, easy to replace the filter element.
4.Imported high performance glass fiber materials
5. Filter house is aluminum alloy material, max pressure is 16bar.