Nitrogen Supply Flexibility
Controlling the airflow through the system will allow you to achieve various flow and purity levels. Future increases in nitrogen demand can be accommodated by adjusting controls or simply adding modules. Our nitrogen membrane systems are versatile and flexible and can operate under extreme temperature and pressure conditions.
The separator's membrane fibers and housing are designed for the most demanding applications. Light weight sensitive applications such as offshore, on board ships and other mobile or remote locations.
How the Nitrogen Membrane Works
The air we breathe is approximately 78% nitrogen, 21% oxygen, and 1% other gases such as argon and water vapor. The system uses this unlimited supply of raw material to produce nitrogen of a specific purity.
Selective permeability is the general principle behind membrane systems. Each gas has a characteristic permeability which is a function of its ability to dissolve and diffuse through the membrane. This property allows separation of "fast" gases (such as oxygen) from "slow" gases (such as nitrogen). The driving force for the separation process is the pressure differential developed between the (compressed) feed air side and the low pressure side of the membrane.
The actual production of nitrogen occurs in the membrane separator. Each separator consists of a bundle of hollow fiber membranes in a cylindrical housing, arranged much like a shell-and-tube heat exchanger. Compressed air is fed into the inlet end of the separator and flows inside the hollow fibers to the other end.
On the way, air molecules start to permeate the fiber walls according to their permeability. Oxygen, carbon dioxide and water vapor permeate faster than nitrogen. The result is an ultra-dry nitrogen flow at the outlet of the separator. A compact membrane separator contains thousands of membrane fibers.
Blower purge desiccant air dryer
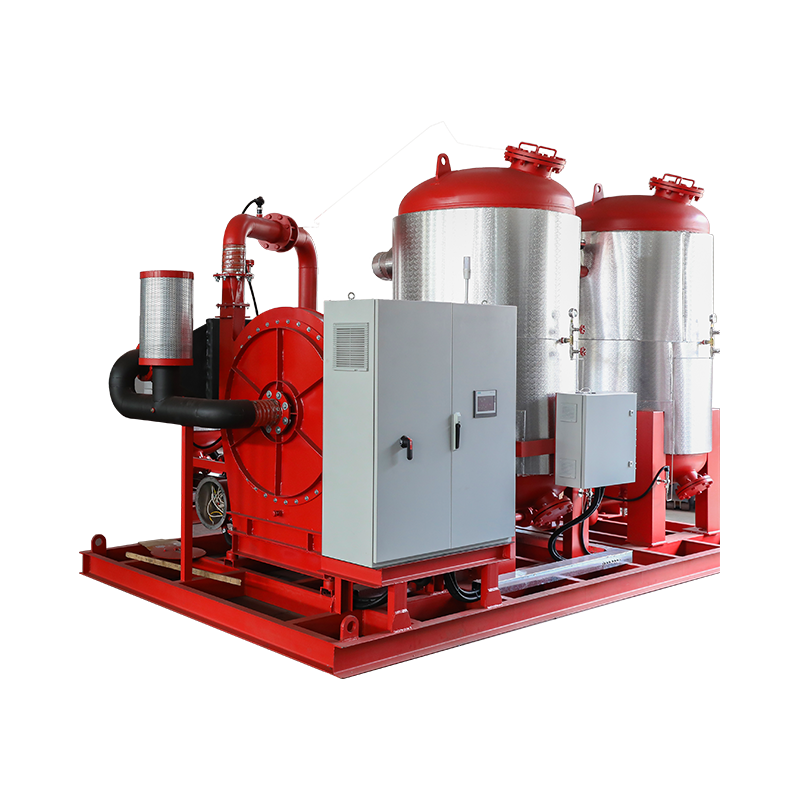
Blower purge desiccant air dryer
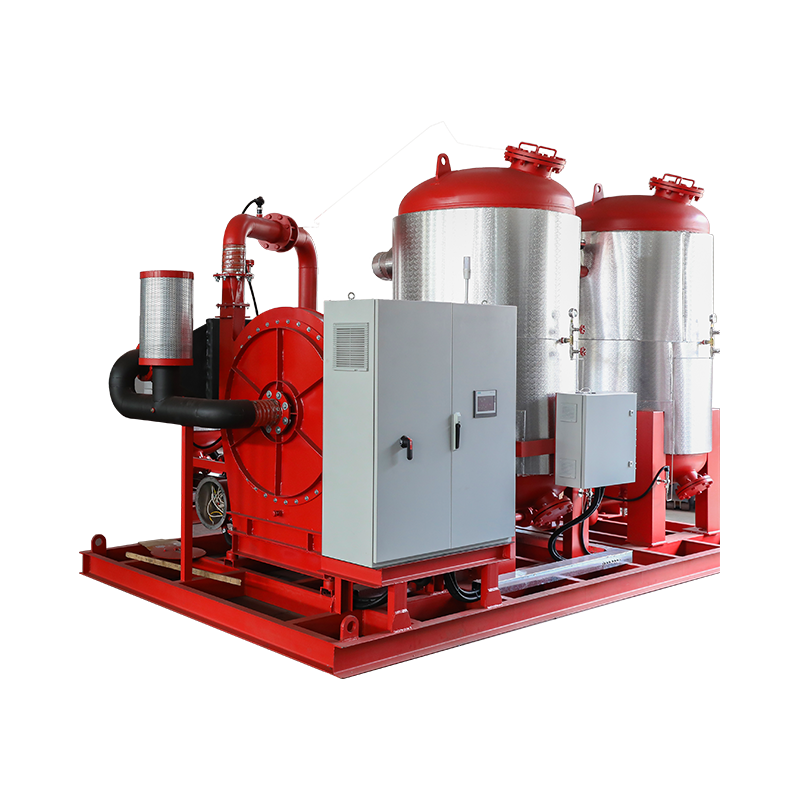
KXB series heated blower purge regeneration air dryer uses air blower and external electrical heater to produce purge air for desiccant regeneration. The blower intakes atmospheric air flow through the heater, then through the desiccant media thereby regenerating it. With this design, no dried compressed air is consumed for regeneration, which maximizes the amount delivered to the air system. Blower heater Air Dryer is usually suitable for large flow from 15 -510m3/min ,2~3% airloss, outlet air pressure dew point is -40~ -70°CPDP. System with Siemens PLC controller, with touch screen,Dew-point sensor.
For higher grade, we also could provide KXP Non purge blower desiccant dryer.